To the untrained eye, people see printing as clicking one button and watching your document slowly edge its way out of your desktop printer. Commercial printing, especially commercially printing labels & Stickers is far from that. There are multiple parts to the process and even these can vary from the print company down to the specific machinery they use. This blog breaks down each step to the Sticker Gizmo printing process which allows us to send out the best bespoke stickers and labels
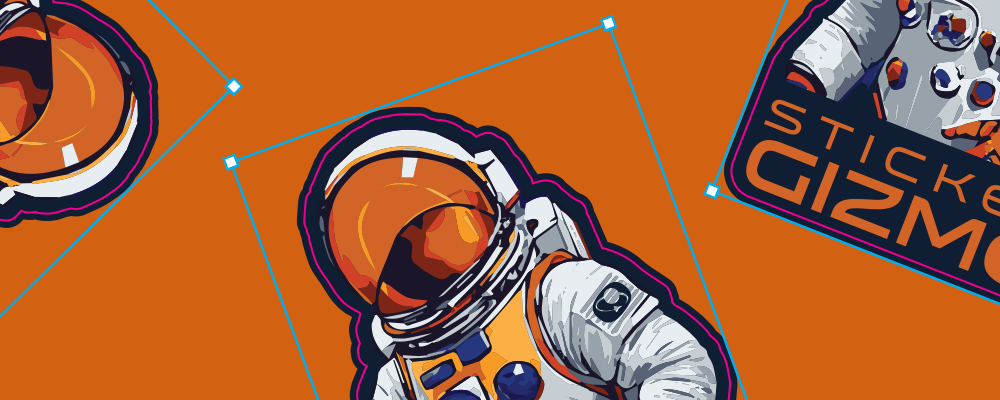
Step One – Artwork
As soon as an order is placed and the customer has chosen their label specification, the first thing to sort out is the artwork. All our customer service crew are experienced graphic designers which means then can very quickly examine your artwork to ensure they are print ready. We follow an internal checklist. Does the artwork have a good enough bleed? Is the artwork vectorised?, Is the artwork set to the correct size? There are many questions like this that need to be answered so our crew can work out what to do next. This will involve them making changes themselves or reaching out to the customer.
We will never send anything to print that we have doubts about. We also take the approach that its better for an order to take slightly longer if necessary. Quality comes first, always. Its also important that you the customer is aware of exactly what is happening.
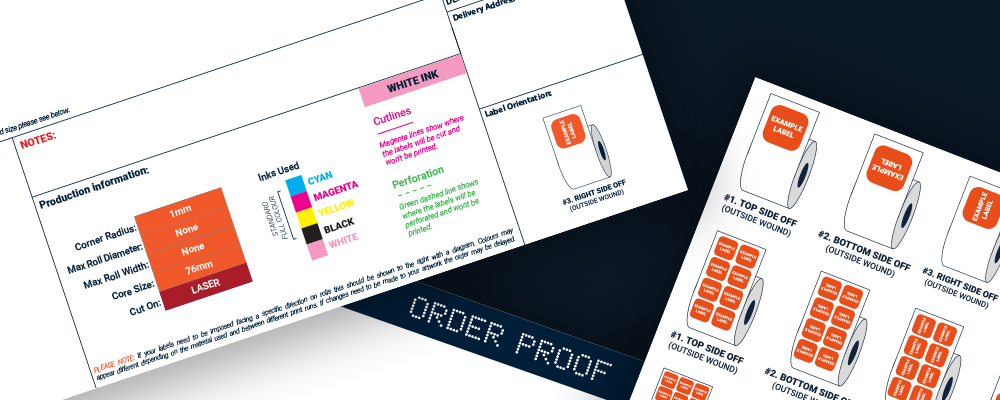
Step Two – Proofing
After our designers have worked their magic, the customer will receive a detailed proof form. This will show all the specifications that were chosen at the point of ordering. We also include any extra information that may have been requested after the time of order. This may include things like the labels orientation on rolls and how many labels per roll. Not only will the print ready artwork be displayed but also a pink line showing where the labels will be cut. Our proof form has gone through many different revisions. We are constantly updating it to improve the customer experience. It’s a fine balance between showing lots of information whilst formatting it in a way that easy for anyone to understand.
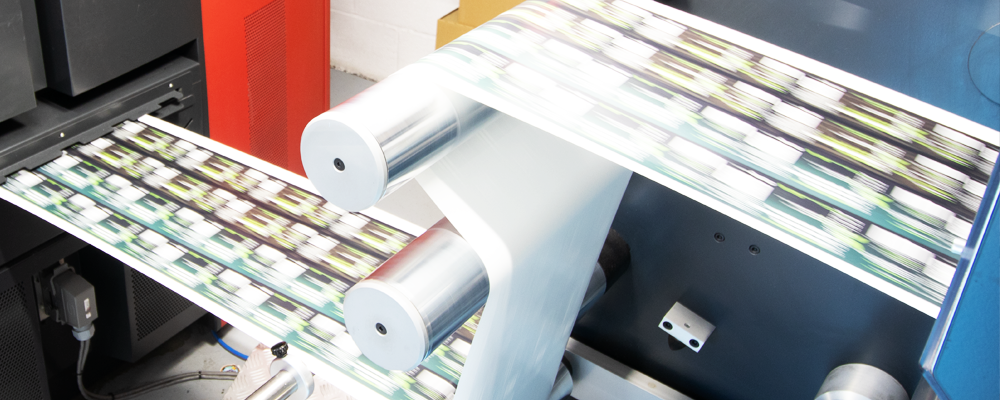
Step Three – Printing
The third step is the main event, printing! After the proof has been signed off by the customer the order is added to our digital print queue. We offer a large range of materials so our print queue is ordered by delivery deadline and material. Once the material is loaded into our printer, we then print all scheduled labels on that material. This leaves us with what is effectively a giant sticker roll with multiple orders on it.
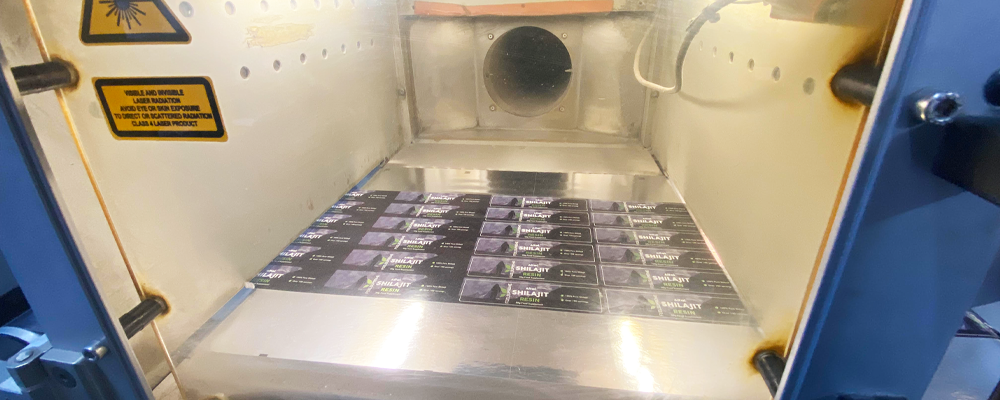
Step Four – Cutting
Once the printing is complete the next stage is for us to cut the labels and peel away the excess label material around the labels. (This is called the ‘matrix’ in the industry). At Sticker Gizmo we can cut labels in a few different ways. If you were to order labels on rolls (our most common way of providing labels) then your labels would be cut with either our Laser cutter or our die cutter.
We choose the cutting machine based on a few factors including the shape, size and quantity ordered. The giant roll I mentioned earlier would effectively be loaded onto the chosen cutting machine. The cutting process used would be shown on your proof form so the customer has complete clarity on how their labels are being finished.
Step Five – Quality Control
QC is a huge part of commercial printing. Although its marked as step 5 in our process, we have multiple quality control points throughout the entire journey. As soon as the first labels are coming out the printer our experienced print team are keeping a close eye on them to ensure the print quality is nothing but perfect. If an issue is spotted, then adjustments would be made instantly to correct the issue. If required, an order would be fully re-printed.
Step Six – Dispatch
Before the labels are packaged they are checked again. This is what we call our last line of defence as its the last opportunity for us to spot any issues before the labels are sent out to the customer. Our dispatch team take a close look at colour, print quality and cut quality. This also involves a peel test to ensure stickers can be peeled away with ease. The dispatch team will also use the same proof sheet the customer is shown as reference.